Introduction
Inventory management is crucial for companies of all sizes in today’s fast-paced business environment. Whether you’re running a small business, managing wholesale operations, or overseeing manufacturing production, having real-time control over your stock levels can make or break your operations. inFlow Inventory Software aims to simplify this process, providing powerful tools designed to streamline inventory management, order processing, and reporting. With a robust set of features, inFlow helps businesses stay organized and efficient.
In this review, we’ll take a deep dive into the key aspects of inFlow, examining its core functionalities, ease of use, and overall value. Specifically, we’ll focus on how inFlow supports manufacturers and wholesalers, helping them maintain an accurate handle on their supply chain, from raw materials to finished goods. By the end of this review, you’ll know whether inFlow is the right inventory solution for your business. If you’re interested in a broader comparison of production management tools, check out our Best Production Management Software guide.
Software Specification
inFlow’s Core Features
inFlow offers an extensive array of features that cater to a wide range of industries, particularly manufacturers, wholesalers, and retailers. Here’s a closer look at some of the most valuable capabilities inFlow provides:
Inventory Management
One of inFlow’s core strengths is its comprehensive inventory management functionality. Businesses can easily track stock across multiple locations, automate stock level updates, and even scan barcodes for quick adjustments. For manufacturers, this means being able to keep track of raw materials, manage stock for various product lines, and minimize disruptions due to out-of-stock situations. inFlow’s system ensures that you always have a clear overview of your current inventory and future needs, preventing costly mistakes and excess stock.
Related features include:
- Multi-location inventory management
- Barcode scanning for faster tracking and adjustments
- Automated reorder points to prevent stock shortages
Order Management
inFlow excels in order management, allowing businesses to seamlessly handle both sales orders and purchase orders. It provides an intuitive process to create, track, and fulfill orders, making it especially helpful for manufacturers and wholesalers managing both production schedules and customer orders.
The integration with various shipping carriers also streamlines the fulfillment process, saving time and minimizing errors. This is particularly beneficial for manufacturers who need to align production with sales orders, ensuring that products are available for delivery at the right time.
Key features include:
- Sales orders management for tracking customer purchases
- Purchase orders for replenishing raw materials and stock
- Shipping integration with major carriers like UPS and FedEx
Manufacturing Features
For manufacturers, inFlow’s features are especially relevant. With Bill of Materials (BOM) management, you can list the components required to build a product and easily track material consumption during production. The software also provides tools for managing work orders, allowing businesses to organize their production workflows more effectively. This ensures that all necessary parts and resources are available for production runs, reducing delays and increasing efficiency.
Key Manufacturing Features:
- Bill of Materials (BOM) to handle raw materials and sub-assemblies
- Work order management to track production stages
- Material tracking from raw materials to finished products
These features position inFlow as a powerful tool for manufacturers looking to improve their production planning and resource allocation.
Reporting and Analytics
Another major benefit of inFlow is its reporting and analytics capabilities. The software comes with a variety of pre-built reports, helping businesses get insights into their inventory levels, sales performance, and order fulfillment. Additionally, users can create custom reports tailored to their specific needs. For manufacturers, this means gaining a better understanding of production efficiency, material usage, and overall profitability.
Key reporting capabilities:
- Pre-built reports for inventory, sales, and fulfillment
- Custom report generation for specialized needs
- Performance tracking to measure KPIs
Integrations
inFlow’s integrations allow businesses to connect their inventory system with other essential software. For accounting, inFlow integrates with QuickBooks, ensuring accurate financial tracking and invoicing. For e-commerce businesses, inFlow can sync with platforms like Shopify to ensure inventory data is updated across all channels in real-time. This flexibility makes inFlow a versatile option for manufacturers and wholesalers who rely on various software systems to run their operations.
Key integrations include:
- QuickBooks integration for seamless accounting
- Shopify integration for syncing eCommerce sales
- API availability for custom integrations
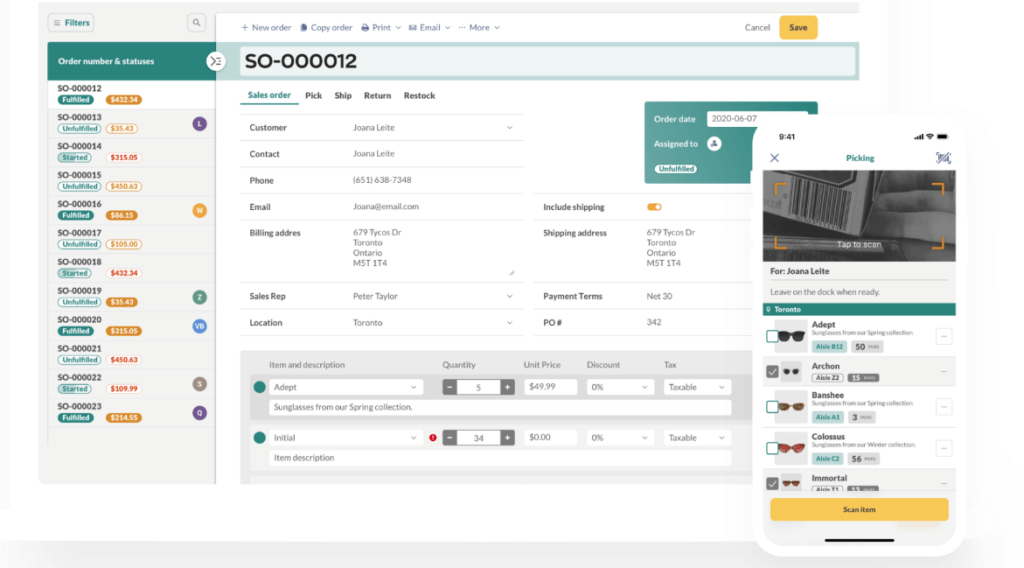
Pros and Cons
Advantages and Disadvantages
Positive
✅ Comprehensive inventory management
✅ Easy to use
✅ Customizable workflow
✅ Seamless eCommerce integrations
Negatives
❌ Limited for large enterprises
❌ Add-on costs
❌ No offline mode
❌ Advanced features require customization
As with any software solution, inFlow Inventory Software comes with both advantages and limitations. Understanding these can help businesses decide whether it’s the right fit for their needs.
Pros
- Feature-Rich for Small to Mid-Size Businesses: inFlow offers a comprehensive range of inventory management features, from basic stock tracking to advanced production planning tools like BOM and work orders. These features are particularly well-suited for small and medium-sized manufacturers and wholesalers.
- Easy to Use: One of the standout benefits of inFlow is its intuitive interface. Whether you’re a small business owner or a warehouse manager, the software is easy to navigate, even for those with minimal technical experience.
- Customizable Workflow: With inFlow, businesses can tailor the software to meet their specific workflows. This customization is essential for businesses that need flexibility in how they manage inventory, orders, and production processes.
- Scalable Plans: From the Entrepreneur plan to the Mid-Size plan, inFlow offers a range of pricing options that scale with your business. This allows smaller businesses to start with a lower-tier plan and upgrade as their needs grow.
- Integration Capabilities: inFlow supports a variety of integrations with accounting software, eCommerce platforms, project management tools, and more. This makes it easy for businesses to connect inFlow to their existing tech stack.
- Great Customer Support: Users consistently report positive experiences with inFlow’s customer service. The combination of live chat, email, and phone support, along with a rich library of documentation and video tutorials, makes it easy to get help when needed.
Cons
- Limited for Large Enterprises: While inFlow is excellent for small to medium businesses, it may not offer the advanced features and scalability required by large enterprises. Larger companies may find the integrations and customizations to be somewhat limited compared to higher-end ERP systems.
- Add-On Costs: Some essential features, like serial number tracking and API access, are available only as add-ons, which can drive up the overall cost for businesses that need these functionalities.
- No Offline Mode: In some industries, especially those with warehouse operations in areas with spotty internet connections, the lack of an offline mode can be a significant drawback. Businesses need to ensure they have a stable internet connection to fully utilize inFlow.
- Learning Curve for Advanced Features: While the core features are user-friendly, some of the more advanced functionalities, like work orders or BOM management, may require additional training or time to master, particularly for teams unfamiliar with this type of software.
User Experience
User Interface and Usability
When it comes to usability, inFlow is known for its intuitive and user-friendly interface. The software’s dashboard offers an organized overview of key metrics such as current stock levels, outstanding orders, and sales performance. Manufacturers and wholesalers can customize the dashboard to display the most relevant data to their daily operations, allowing them to make informed decisions in real-time.
One of the highlights of inFlow’s design is its simplicity. Even users without extensive technical experience can quickly learn how to navigate the system. The interface is clean, with all critical features easily accessible through a sidebar menu. Each section of the software, whether you’re managing inventory, generating reports, or creating purchase orders, follows a logical flow, minimizing the learning curve.
For those who need mobility, inFlow’s mobile app provides access to key features on the go. This is especially useful for field teams and warehouse staff who need real-time updates on stock levels or orders while working away from the desktop interface.
Customization is another notable strength. Users can tailor their workflows and dashboards to match their specific needs, whether they’re managing complex manufacturing processes or simpler wholesale operations. This flexibility helps businesses maximize the utility of the software without overwhelming users with unnecessary features.
Key takeaways:
- Intuitive interface with a minimal learning curve
- Mobile app for on-the-go management
- Customizable workflows to fit specific business needs
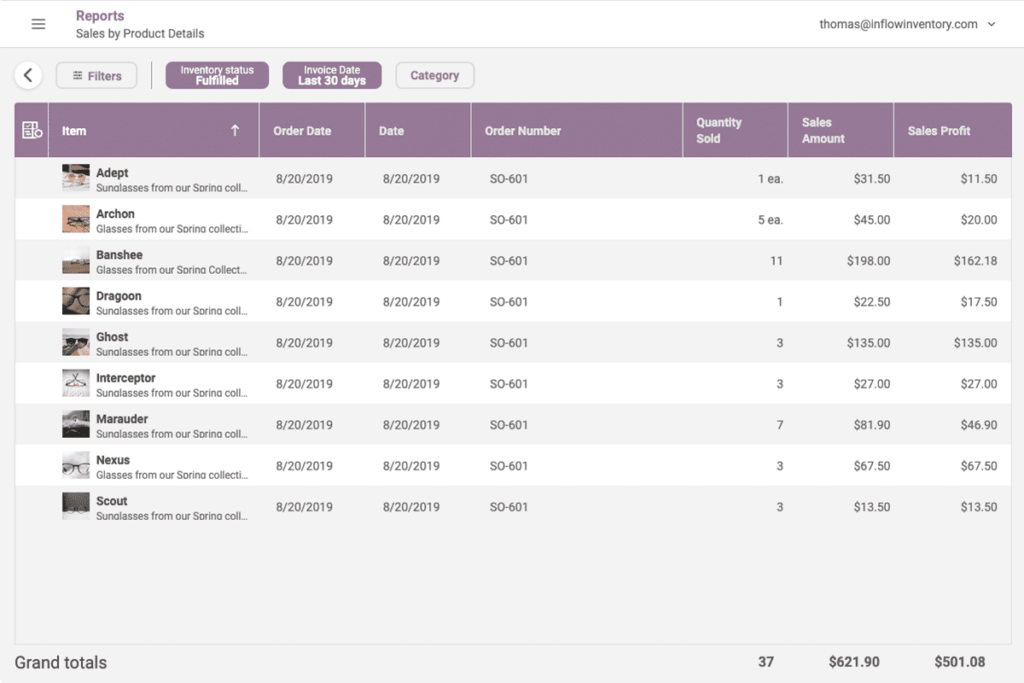
Top Benefits
How inFlow Benefits Manufacturers and Wholesalers
For manufacturers and wholesalers, efficient inventory control and production management are essential for staying competitive. inFlow Inventory Software provides features that directly address these needs, making it a standout solution in the market.
Inventory Control
Manufacturers often deal with large quantities of raw materials and finished goods, and effective inventory control is critical. With inFlow, businesses can monitor stock levels in real-time, helping to reduce the risks of overstocking or understocking. The software’s automated reordering system ensures that materials are reordered when stock levels hit a predefined minimum, helping manufacturers avoid delays in production due to missing parts or materials.
Additionally, inFlow supports multi-location tracking, allowing businesses to monitor inventory across several warehouses or production facilities. This feature is especially beneficial for wholesalers and large-scale manufacturers with complex supply chains.
Order Fulfillment
inFlow’s order management tools are a boon for businesses handling both production orders and customer orders. Manufacturers can synchronize their inventory system with sales and purchase orders, ensuring that products are available when needed and that customer orders are fulfilled efficiently. The seamless integration with shipping carriers like FedEx and UPS helps automate the fulfillment process, from picking and packing to shipping and tracking.
This streamlined order process reduces the chance of errors and delays, leading to improved customer satisfaction and more efficient operations.
Production Planning
Manufacturers need tools to help them plan production runs and manage the flow of materials. inFlow offers support for work orders and Bill of Materials (BOM) management, giving manufacturers the tools to organize and track production workflows. By keeping a close eye on the availability of raw materials and the progress of production, businesses can minimize downtime and ensure that production stays on schedule.
These production planning tools help manufacturers optimize their processes, ensuring that they have the right materials at the right time, reducing waste and inefficiencies.
Cost Tracking
Accurate cost tracking is essential for profitability in manufacturing. inFlow helps businesses track the cost of raw materials, labor, and overhead costs associated with production. This information can be used to adjust pricing, calculate profit margins, and ensure that the business is operating efficiently. By keeping a close eye on costs, manufacturers can make informed decisions that help improve profitability.
Pricing and Packages
Pricing and Plans for inFlow
inFlow Inventory Software offers a tiered pricing structure that caters to businesses of different sizes, from startups to larger manufacturing and wholesale operations. Here’s a breakdown of the pricing plans and what each offers:
Entrepreneur Plan – Starting at $89/month (billed annually)
- Team members: 2
- Sales orders: Up to 1,200 orders per year
- Integrations: 1 integration
- Inventory locations: 1 location, no sublocations
- Setup assistance: 2 hours
This plan is ideal for small startups or solo entrepreneurs managing basic inventory needs. It provides enough features to handle basic inventory tracking and order management, but may lack the advanced capabilities required by larger operations.
Small Business Plan – Starting at $219/month (billed annually)
- Team members: 5
- Sales orders: Up to 12,000 orders per year
- Integrations: 2 integrations
- Inventory locations: Unlimited
- Setup assistance: 4 hours
- User access rights
- Optional API access (add-on)
- Serial numbers (add-on)
This is the most popular plan, offering a good balance between price and functionality. It is well-suited for small to medium-sized businesses with moderate inventory and order management needs. The inclusion of user access rights and the option to add API access makes it more flexible for businesses looking to integrate inFlow with other systems.
Mid-Size Plan – Starting at $439/month (billed annually)
- Team members: 10
- Sales orders: Up to 60,000 orders per year
- Integrations: 3 integrations
- Inventory locations: Unlimited
- Setup assistance: 6 hours
- Advanced user access rights
- Optional API access (add-on)
- Showroom Pro
- Serial numbers (add-on)
- Single sign-on (SSO)
The Mid-Size Plan is ideal for larger companies with higher volume requirements. It provides more advanced features like single sign-on (SSO) and Showroom Pro, making it a great fit for businesses that need enhanced security and showroom management capabilities.
Each of these plans offers the flexibility to purchase add-ons like API access and serial number tracking, allowing businesses to customize the software to meet their specific needs.
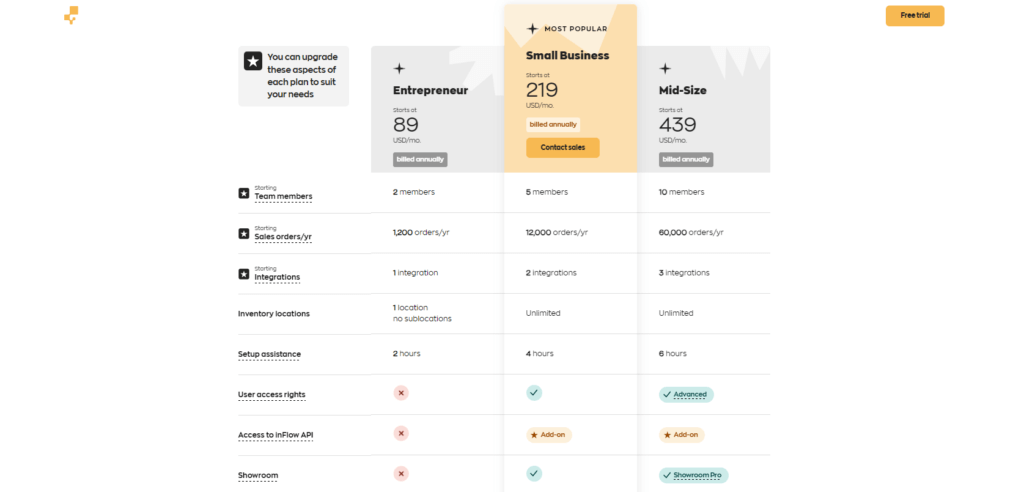
Integrations
Connecting with Other Tools
inFlow integrates seamlessly with a variety of other work management tools, allowing businesses to synchronize their inventory system with other essential platforms. Here’s a look at some of the most important integrations:
Project Management Tools
Manufacturers and wholesalers often rely on project management software like monday.com or Asana to manage tasks, track production schedules, and collaborate on projects. inFlow integrates with these tools, enabling teams to connect inventory management with project timelines, ensuring that the right materials are available when needed for specific projects or orders.
Accounting Software
Keeping your books in order is essential for any business, and inFlow’s integration with QuickBooks makes financial tracking easy. By syncing inventory data with accounting software, businesses can ensure that inventory costs, sales, and purchases are accurately reflected in their financial reports. This reduces the chance of errors and simplifies tax preparation.
eCommerce Platforms
For wholesalers and manufacturers selling products online, inFlow integrates with popular eCommerce platforms like Shopify and WooCommerce. This integration keeps inventory data updated in real-time, ensuring that your online store always reflects accurate stock levels. When a sale is made online, inFlow automatically updates your inventory, reducing the risk of overselling products.
Custom Integrations
For businesses with unique needs, inFlow offers API access (available as an add-on) that allows for custom integrations. This is particularly useful for larger manufacturers or wholesalers who need to connect inFlow to proprietary systems or specialized tools used in their industry.
Customer Service
Customer Support and Resources
inFlow is well-regarded for its customer support, offering multiple channels for businesses to get the help they need. Whether you’re new to the software or an experienced user, inFlow’s support team is readily available to assist with any issues that may arise.
Support Channels
- Live chat: Fast and responsive, live chat support is available for quick inquiries and troubleshooting.
- Email support: For more detailed questions or problems, email support is available with reasonable response times.
- Phone support: Businesses on higher-tier plans may benefit from direct phone support, offering a more personalized level of service.
Self-Help Resources
inFlow also provides a range of self-help resources to empower users to resolve issues on their own:
- Documentation: Extensive online documentation is available, covering all aspects of the software.
- Video tutorials: Step-by-step videos walk users through common tasks and features.
- Community forums: Users can connect with others to share tips, ask questions, and learn from the experiences of other inFlow users.
Overall, inFlow’s customer support is robust, offering businesses multiple ways to get assistance and solve problems quickly.
Conclusion
Final thought
After an in-depth review of inFlow Inventory Software, it’s clear that this platform offers a solid solution for businesses looking to improve their inventory management processes. inFlow excels in delivering features that are essential for manufacturers, wholesalers, and retailers alike. Its intuitive interface and ability to scale from small operations to more complex workflows make it a strong contender in the inventory management space.
Who Should Consider inFlow?
- Small to Mid-Sized Manufacturers: For manufacturers managing raw materials, work orders, and production schedules, inFlow provides the necessary tools to streamline operations, track costs, and optimize stock levels.
- Wholesalers and Retailers: With robust order management capabilities, inFlow can handle large volumes of sales and purchase orders, making it an excellent choice for wholesalers and retailers who need real-time inventory tracking across multiple locations.
- Growing Businesses: inFlow’s tiered pricing plans make it a great option for businesses that expect to scale. You can start with a basic plan and gradually move up as your business needs grow.
Who Might Look Elsewhere?
- Large Enterprises: Companies that require more complex customizations, integrations, or enterprise-level features may find inFlow limiting. In such cases, an ERP system with more comprehensive capabilities might be a better fit.
- Businesses Needing Offline Access: If you operate in an environment with limited internet connectivity, the lack of offline access could be a dealbreaker.
In conclusion, inFlow Inventory Software is an excellent choice for small to medium-sized businesses that need a reliable, feature-rich, and easy-to-use inventory management tool. With its flexibility, scalability, and robust support, inFlow can significantly improve your inventory and order management processes. If you’re exploring other production management tools, be sure to check out our Best Production Management Software comparison for more options.
Have more questions?
Frequently Asked Questions
Does inFlow work offline?
No, inFlow does not currently offer an offline mode. Users must have an active internet connection to use the software.
What industries does inFlow serve?
While inFlow is used across various industries, it is particularly popular among manufacturers, wholesalers, and retailers. The software is versatile enough to handle the inventory needs of both product-based businesses and service providers that need to manage parts and materials.
How does inFlow handle multi-location inventory?
With inFlow, you can track inventory across multiple locations, making it easier for businesses with more than one warehouse or distribution center to stay organized. This feature is available starting with the Small Business plan and above.
What integrations does inFlow support?
inFlow integrates with popular tools such as QuickBooks, Shopify, WooCommerce, and project management platforms like Asana. Additionally, businesses can use the API add-on to create custom integrations with other systems.
Can I track serial numbers with inFlow?
Yes, but serial number tracking is an optional add-on. This feature allows businesses to track individual products and components by their serial numbers, which is particularly useful for warranty tracking, product recalls, and compliance requirements.
Is inFlow an ERP?
No, inFlow is not a full ERP (Enterprise Resource Planning) system. While it offers many of the features typically found in ERP systems, such as inventory management, order processing, and basic manufacturing tools, it does not cover other areas like human resources or advanced financial management that are usually part of an ERP solution. inFlow is more focused on inventory management and order tracking for small to medium-sized businesses rather than providing an all-encompassing suite of enterprise tools.
Is inFlow Inventory cloud-based?
Yes, inFlow Inventory is a cloud-based software, allowing businesses to access their inventory data from anywhere with an internet connection. The cloud-based nature of inFlow ensures that inventory data is always up to date in real-time across all devices, making it ideal for businesses that operate in multiple locations or have remote teams.
Is inFlow Inventory free?
inFlow Inventory offers a free plan known as inFlow On-Premise, which is limited in functionality but can be used for smaller operations or businesses that want to test the software before upgrading. The free version allows for a limited number of products and users, but upgrading to one of the paid plans (like the Entrepreneur, Small Business, or Mid-Size plans) unlocks additional features such as multi-location tracking, integrations, and advanced reporting.
What is the difference between inFlow Inventory and inFlow Manufacturing?
The primary difference between inFlow Inventory and inFlow Manufacturing is in the scope of features offered. While both versions include robust inventory management tools, inFlow Manufacturing adds specific features designed for manufacturers, such as Bill of Materials (BOM) management, work orders, and production tracking. These additional features are tailored for businesses that need to manage not just inventory but also the production process, from raw materials to finished goods.